Words & Pics: Dan Maslic
Does more boost really lead to more horsepower? The answer is yes and no, depending on the circumstances and the engine and parts combo in question. We’ve heard it before: A little puffer gets bolted onto a hot-rod and the car makes great power. More power is great, but it’s never enough, so on goes a smaller pulley for more boost and thus more power. Success! Then, in the quest for more speed still, an even smaller pulley goes on and there’s more boost still, but power seems to have leveled off or perhaps even drops. What gives?
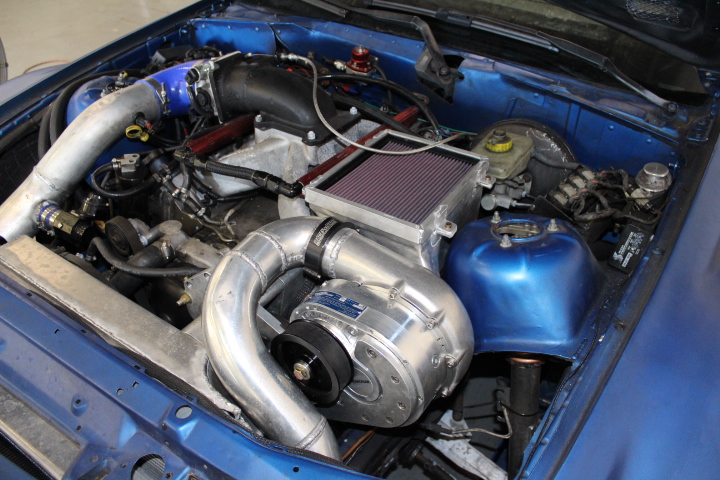
The answer is that more boost doesn’t necessarily mean more power. When air is compressed, its temperature rises. When the temperature of air rises in a given volume, the pressure within that volume increases. If the volume increases but the temperature remains fairly constant, the air pressure drops but the air density and thus the air mass per volume decreases. This is why intercoolers (or chargecoolers as they’re called by engineers) exist. The purpose of an intercooler/chargecooler is to decrease the temperature of the air mass entering the engine and thus increase the air density and thus allow a greater mass of air to fill the cylinders during the intake stroke. More air allows more fuel to be burned and that allows a higher mean cylinder pressure which results in more torque and horsepower. Simple, really.
So then, the answer to our original question must be “just use a larger intercooler”, right? Well, no. If you take a look at the following screenshot below, you’ll see that the intake air temperature here is 154 degrees F. This is the data captured while running on a racetrack. You can see that engine speed is 6569 RPM (the speedo isn’t hooked up here). Boost is approximately 5.0 psi (135 kPa MAP pressure).
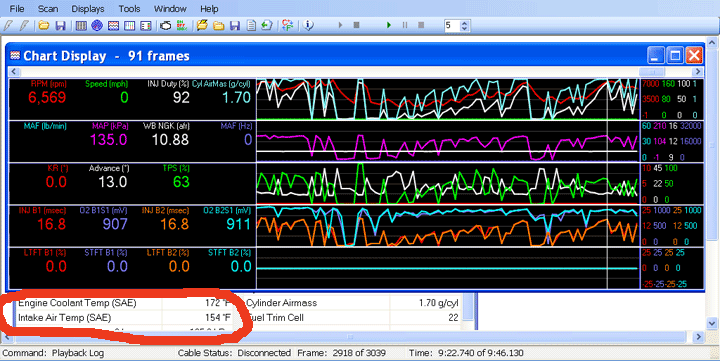
When the car is run again during the next session, the results below get worse. Again, engine speed is similar at 6556 RPM while the intake air temperature has increased to 196 degrees F. The MAP pressure is still similar at 139 kPa, just over 5.5 psi of boost.
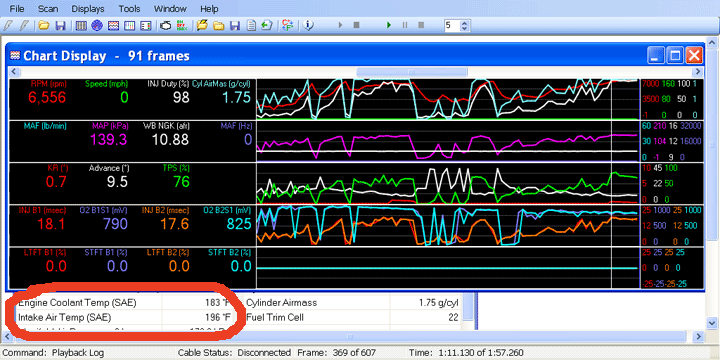
The answer here actually lies in compressor efficiency. Sizing the supercharger correctly for the given amount of air mass flow one needs to create the power necessary is vital. You can only spin a supercharger up so fast before you start operating out of the supercharger’s best window of efficiency. An example of such a compressor map is below:
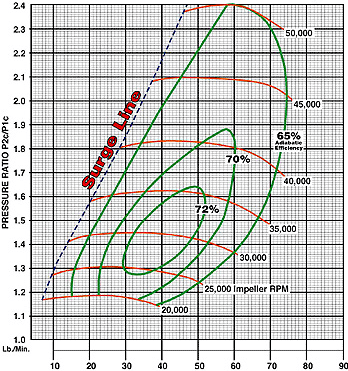
The compressor map above illustrates that at about 7 psi of boost (1.5 pressure ratio on the y-axis) you’ll land in the 72% efficiency range between 35-50 lbs/min of air mass flow (enough for about 500 hp). At that pressure ratio, the supercharger in question here would be spinning at approximately 32,500 RPM. If the engine didn’t move air as easily and the supercharger had to spin at 43,000 RPM to move the same amount of air through the engine and make the same horsepower, the compressor efficiency would drop down to 65%, a loss of 7% efficiency. This will, of course, also be reflected in the intake air temperature as it will increase due to the reduced efficiency. Asking the supercharger to crank out enough air for 800 hp would put the efficiency down into the low 60% range. In other words, a bigger blower would be a better bet as it would run more efficiently and not add as much heat to the intake air as it compresses it.
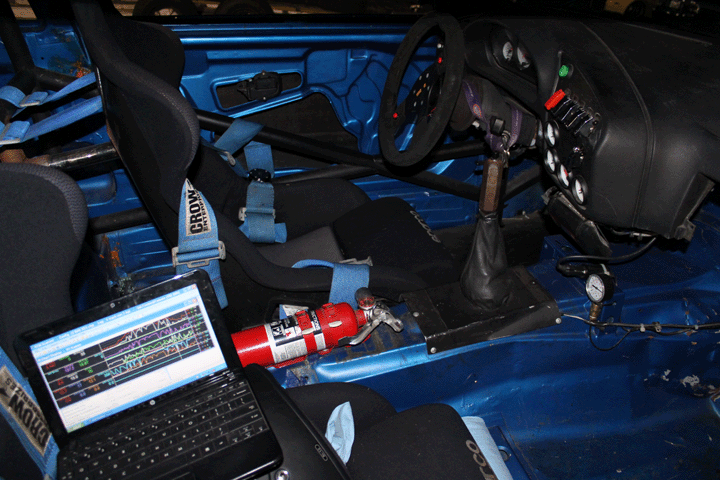
Once you’ve swapped the old, smaller blower out for a nice big puffer, you can hit the track again and test and tune.
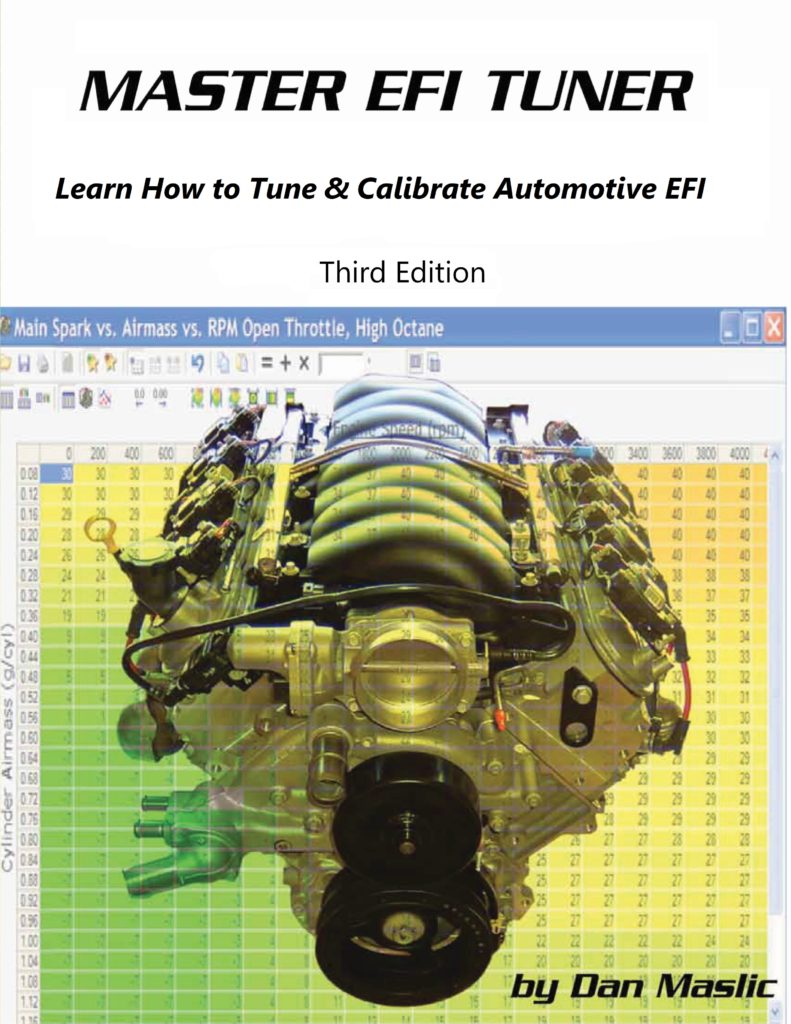